The precise adjustment of your laboratory test sieve shaker to the material to be sieved often determines the success or failure of your test sieving. With three-dimensional test sieve shakers, you control the sieve setting primarily via three parameters:
With the right amplitude setting, the well-regulated use of the interval mode and the optimum sieving time, you can easily standardize your sieving process and rely on reproducible sieving results.
What does the amplitude do?
When sieving, it is important that each particle has the opportunity to pass through a free sieve opening as often as possible. This is the case when the particles briefly lift off once with each vibration of the test sieve shaker and fall onto a neighboring free sieve mesh. The three-dimensional sieving should also allow the particles to rotate and hit the sieve opening in any possible orientation.
A good example of this effect is a flat grain: it can pass through a square sieve opening if it hits an opening on edge or diagonally, which would be too small for the flat grain if it hit it horizontally.
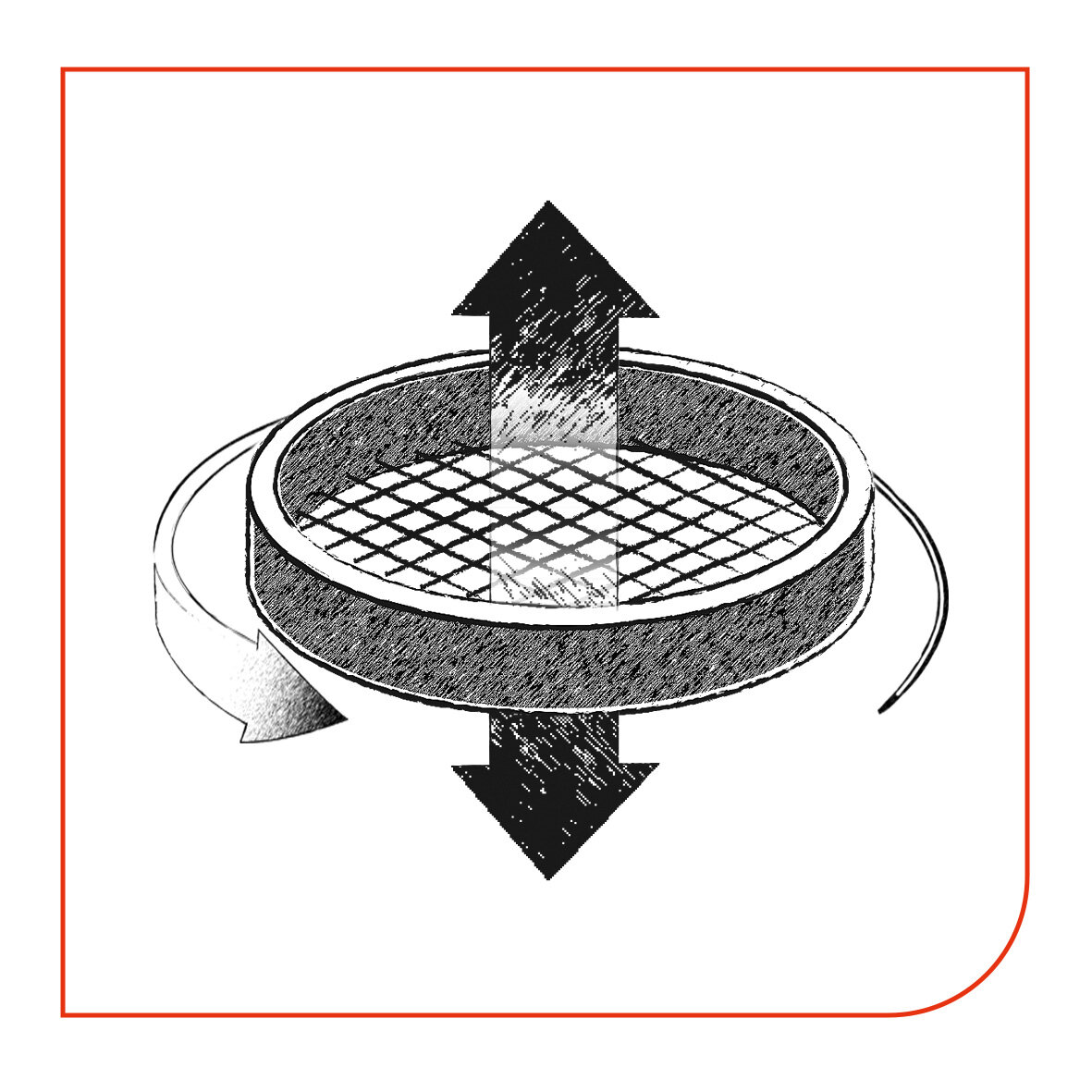
In three-dimensional sieving, a throwing motion is simulated by accelerating the particles through the up and down impulse of the sieving machine and directing them into a parabolic trajectory through the simultaneous rotary motion of the sieve tower. The acceleration of the particles depends on the amplitude of the up and down pulse. If a high amplitude is selected, the acceleration is stronger and larger particles can also be lifted out of the sieve mesh.
However, if very light and small particles are to be sieved, a high amplitude can cause the particles to float in the air for a very long time. Under such conditions, the time required to reach the sieving point is extended. Furthermore, with fragile materials, there is a risk that the particles will be destroyed or subject to abrasion if the amplitude is too high and thus lose size.
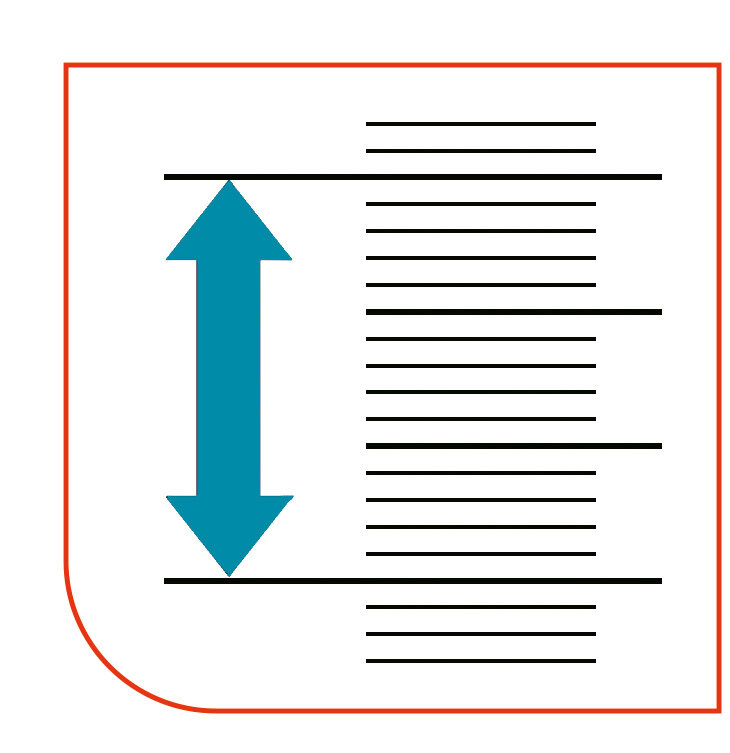
Rule of thumb: “As small as possible - as large as necessary”
Generally speaking, it can therefore be said that the lowest possible amplitude setting true to the motto “as small as possible - as large as necessary” is a good choice. A sieving machine with self-regulating amplitude is recommended for such standardization. Regardless of the feed weight of the sieving material or the sieving tower, the electronics of the sieving machine regulate the strength of the magnetic pulse so that the preselected amplitude is constantly maintained. This ensures that the test parameters do not change with the same machine setting.
The set amplitude can be easily assessed through the inspection glass of the sieve cover. Fine particles further down in the sieve tower are often thrown much higher than the particles on the upper test sieves. For this reason, you should briefly remove the coarse sieves after a certain sieving time to check and get an impression of the material movement on the fine sieves through the sieve cover. Your aim should always be to ensure that the sieve material on the sieves with the largest sieve backlog and therefore the fewest free sieve meshes is moved under optimum conditions.
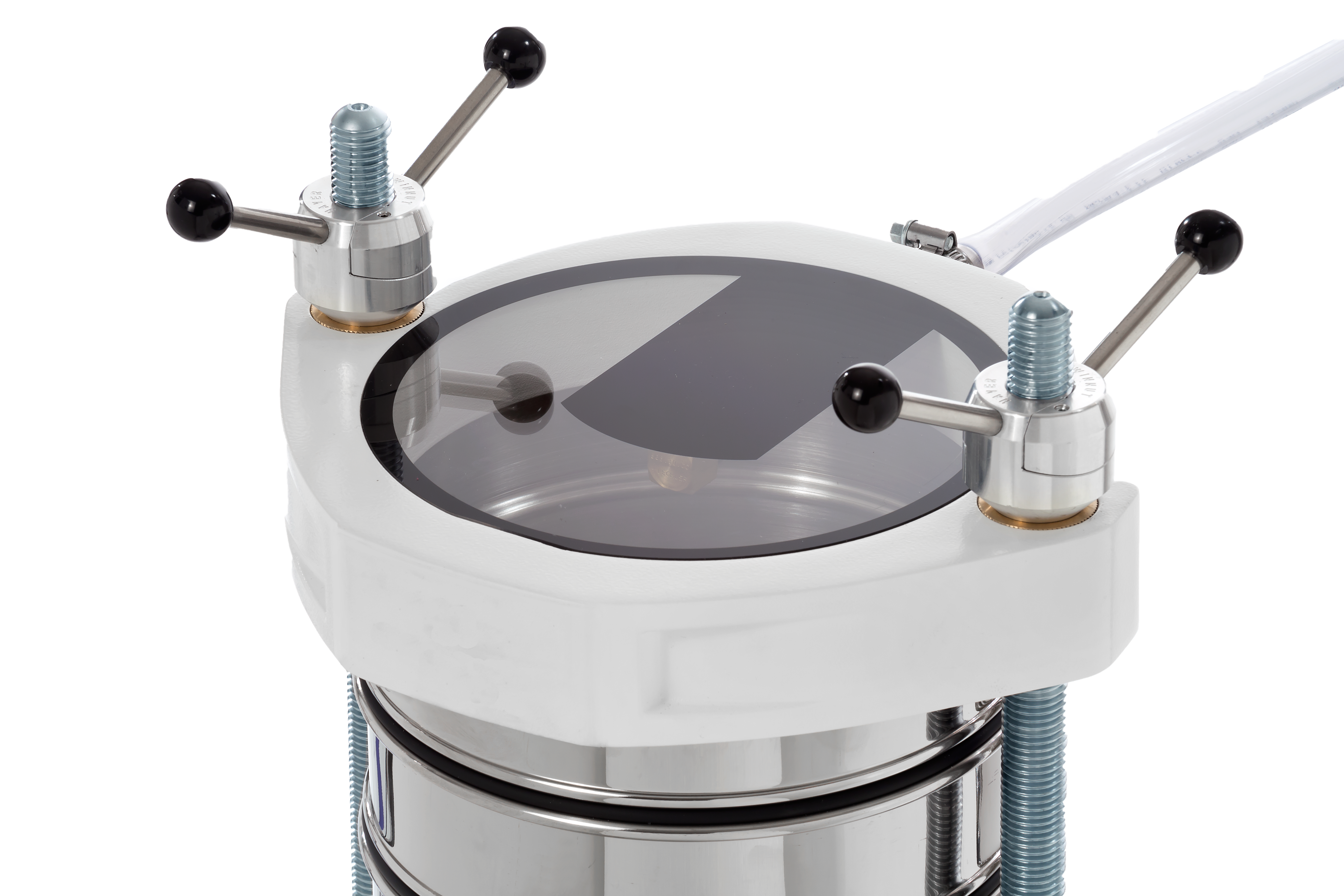
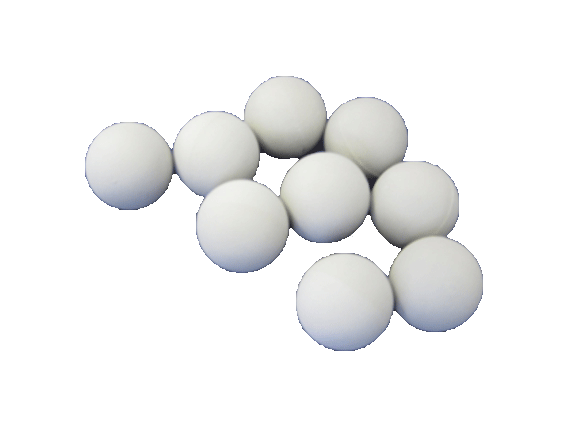
Special case of sieving tools
You may use sieving tools (e.g. rubber tapping balls) to loosen jammed particles from the sieve mesh if the standard applicable to your product explicitly provides for this. In these cases, a higher amplitude is sometimes necessary to make the rubber balls bounce. You should insert the rubber tapping balls in an additional test sieve with a significantly larger mesh size under the clogged sieve. This ensures that the tapping balls only hit the mesh from underneath and that trickling material can quickly pass through the additional sieve layer without being destroyed by the tapping balls.
Sieving in interval mode: ideal for abrasive and fine materials
There are many different critical materials that make sieving very difficult. For example, highly abrasive materials tend to jam in the sieve mesh and quickly clog the test sieve. As described above, other materials are so light that the particles float almost constantly in the air during sieving. For such applications, the electromagnetic test sieve shakers have an interval mode. The set interval time determines the operating time after which sieving is interrupted for one second. This also gives the fine material, which is mainly suspended during the screening process, the opportunity to fall onto the sieve and find an open mesh. At the same time, the strong start-up acceleration after the interval pause loosens jammed material. This efficiently prevents your sieves from clogging in many applications.
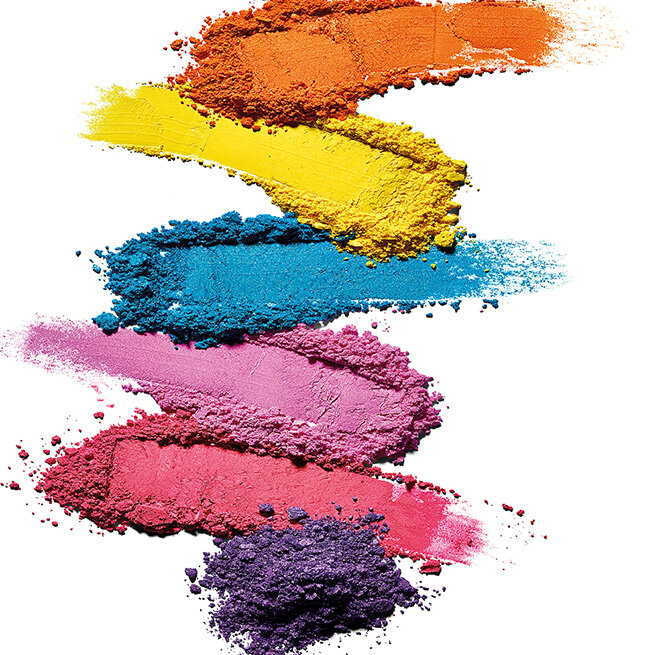
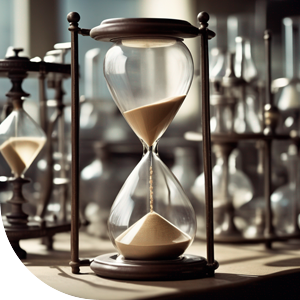
Setting the optimum sieving time
With regard to the optimum sieving time, it should be noted that the end point of a sieving process is only reached when the throughput value of a material changes by less than 0.1 % within one minute (see DIN 66165 standard). Depending on the nature of the material, this point may be reached after just a few minutes or even after an hour.
The optimum sieving time is often specified in the norm - alternatively, you can systematically test different sieving times and then check the result by hand sieving. Especially when defining standard sieving parameters, this step can save you valuable time in future everyday analysis sieving.